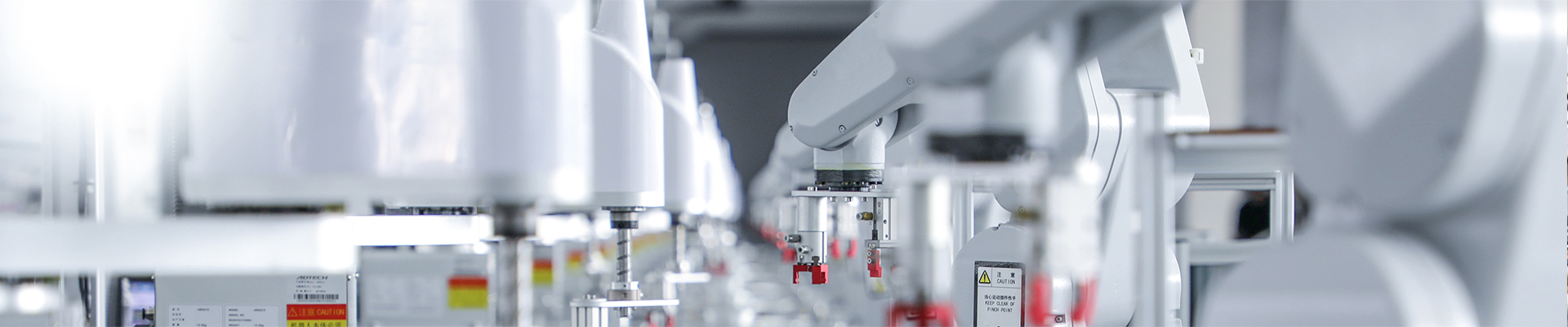
Projection welding nut error proofing detector: a masterpiece to improve welding quality and efficiency
2025-03-08 15:50In fast-paced industrial production, the correctness of projection welding nut welding is undoubtedly a key link to ensure product quality and production efficiency. As an outstanding representative of modern welding technology, the projection welding nut error proofing detector (welding management instrument) has injected strong power into the production process with welding detector's excellent performance and rich functions.
This advanced welding detector uses a programmable controller as the control core and takes precision technology as the cornerstone to ensure the foolproof welding of projection welding nuts. Through the precise pressurization of the welding machine's pressurized cylinder, the lower electrode positioning pin is steadily pressed down for position determination. During the detection process, the detector will quickly read the current nut position information and make a detailed comparison with the preset allowable position. Once the position is correct (OK), welding detector will be powered on immediately for welding; if the position is wrong (NG), the pressurized cylinder will be decisively disconnected to prevent power from being turned on, and a clear alarm indication (type B) will be issued, thereby completely eliminating the occurrence of welding errors at the source.
The welding counting function of the projection welding nut error proofing detector is also impressive. Welding testing equipment can not only accurately record the number of projection welded nuts, but also count the number of electrode exchanges, the number of units produced, and the life of the positioning pins. These counting signals can be flexibly provided by a variety of devices such as proximity switches, photoelectric switches, travel switches, micro switches or relays, and are not limited by distance, which greatly improves the convenience of production management. In addition, the function of adding points meets the diversified production needs, making production more flexible and efficient.
In terms of operational convenience, this projection welding nut error proofing detector also performs well. Projection welding nut error proofing detector's interface design is humanized, with a clear welding parameter table and component name display, so that operators can quickly confirm the welding conditions when changing workpieces, greatly improving work efficiency. At the same time, the reset operation of counting and nut welding abnormality supports both manual and automatic modes, providing more flexible options for production management. When the welding count reaches the set value or a welding abnormality is detected, if the automatic reset mode is selected, the time of automatic reset can be freely set, further improving the automation level of the production line.
For factory site managers, the projection welded nut error proofing detector is undoubtedly a powerful assistant. Projection welding nut error proofing detector can effectively prevent the occurrence of problems such as leaking welding and excessive welding, and eliminate the phenomenon of product scrapping due to welding errors, making the production process smoother and more orderly. By improving work efficiency and ensuring product quality, this detector has brought significant economic and social benefits to the production and operation of enterprises, and has become an indispensable high-quality equipment in industrial production. On the road of pursuing high-quality and high-efficiency industrial production, the projection welding nut error-proofing detector is undoubtedly a sharp sword, helping enterprises to overcome difficulties and climb to new heights.