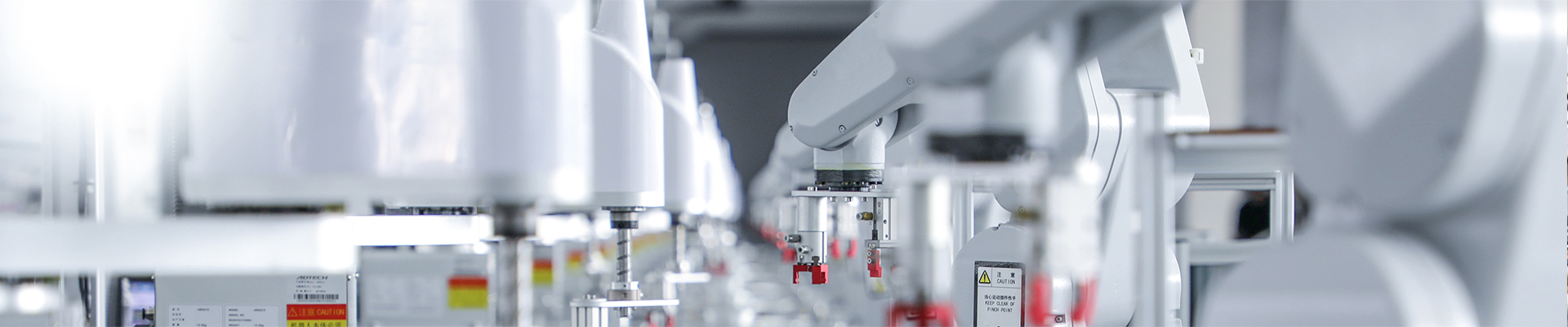
Application and technological innovation of precision spot welding machine in nut welding
2025-03-15 19:22With the improvement of precision and reliability demands in manufacturing for connectors, precision spot welding machines have become crucial in nut welding due to their high accuracy, low damage, and stability.Especially in high-demand industries such as automotive manufacturing and aerospace, the combined application of panel spot welding machines with nut anti-reversal technology and high-precision welding power supply has significantly improved production efficiency and product qualification rate.
Core Technical Characteristics:
Microsecond Control Accuracy: Uses high-frequency inverter DC power supply (up to 25kHz) for a 0.2ms current response. DSP controls adjust welding parameters for uniform weld formation, preventing deformation or damage.
Multi-stage Welding & Spatter Control: Supports multi-stage discharge (preheating, slow rise, welding, slow fall) to reduce spatter, achieving a <0.5% spatter rate in auto exhaust welding.
Servo Pressure Control: Dynamic adjustment of welding pressure (±1N accuracy) ensures stable nut-workpiece contact, boosting pull-out strength to 90% of parent material.
Quality Control: Supports pressure limits and trigger welding. Displacement penetration ensures welding consistency. Standard proportional valve controls air pressure stability.
Nut Anti-reverse Technology:
Dual Anti-reverse: Mechanical positioning and electrical signal detection ensure nut direction accuracy. Location pin and insulation sleeve mechanisms prevent reverse nuts from welding.
Automated Integration: Combined with vision recognition or vibration plate conveying, the anti-reverse device ensures 100% nut direction verification, boosting detection to 99.8%.
High-precision Welding Power Supply Upgrade:
Six Control Modes: Supports constant current, voltage, and power modes for various materials like copper, aluminum, stainless steel.
Real-time Monitoring: Built-in database records welding parameters (up to 100,000 entries), supports U-disk export. Waveform oscilloscope displays 8 welding curves for quick fault diagnosis.
Thermal & Environmental Management: Water-cooling keeps electrode temp <50°C, reducing the heat-affected zone. Low-smoke technology decreases workshop pollution.
Applications & Benefits:
Automotive: Automated welding of engine bracket nuts with ≤0.5s per point, 99.5% yield.
Electronics: Welds circuit board shielding covers with ≤0.1mm diameter error, meeting micron-level assembly.
Future Trends:
AI Integration: Adaptive optimization of welding parameters.
IoT Monitoring: Remote equipment status monitoring for intelligent manufacturing upgrades.