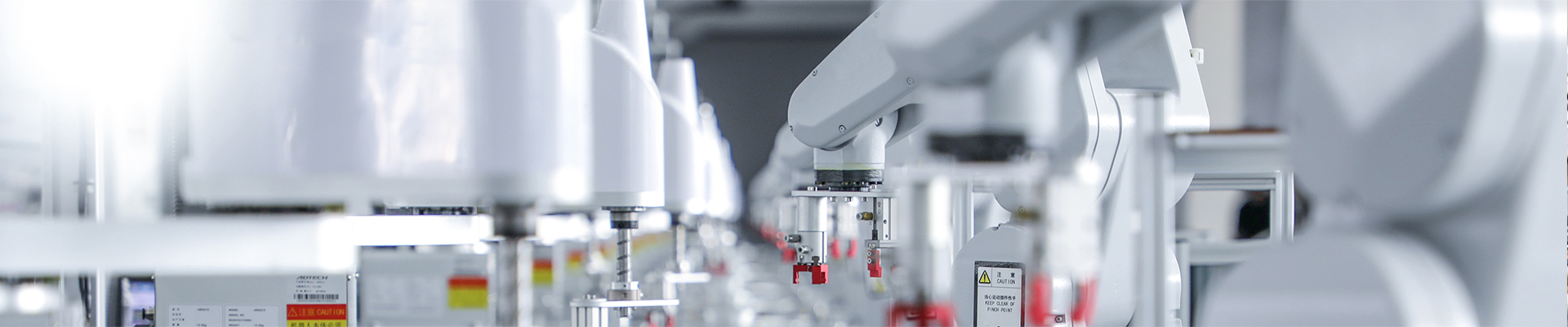
How to choose electrode material for precision spot welding machine?
2024-10-11 15:26Selection of electrode materials and shapes for precision spot welding machines: analysis of key factors
In the vast field of resistance welding, the electrode materials and shapes of precision spot welding machines play a vital role. They are directly related to the quality of welded parts, production costs and labor productivity. Therefore, in production practice, we must pay enough attention to these two factors. In view of the wide application, harsh working conditions and diverse varieties of spot welding precision spot welding machine electrodes, this article will focus on a detailed introduction.
1. Chrome zirconium copper (CuCrZr): cost-effective choice
As a common material for resistance welding electrodes, chrome zirconium copper has won wide recognition for its excellent chemical and physical properties and extremely high cost-effectiveness.
Performance balance: Chrome zirconium copper electrodes perform well in conductivity, high-temperature mechanical properties, wear resistance, hardness and strength, achieving a perfect balance of the four performance indicators of welding electrodes. This ensures that the impedance of the welding circuit is small, thus obtaining excellent welding quality; at the same time, the higher softening temperature ensures the performance and life of the electrode in a high temperature environment; the wear resistance extends the service life of the electrode and reduces the cost; and the higher hardness and strength ensure that the electrode head is not easily deformed and crushed under pressure, further ensuring the welding quality.
Cost-effectiveness: As a consumable in industrial production, the amount of electrodes used is large, so the price cost is also an important consideration. While maintaining excellent performance, the price of chromium-zirconium-copper electrodes is relatively affordable and can fully meet production needs.
Scope of application: chromium-zirconium-copper electrodes are suitable for spot welding and projection welding of parts such as carbon steel plates, stainless steel plates, and coated plates, and can manufacture a variety of electrode parts such as electrode caps, electrode connecting rods, and electrode heads. Through cold extrusion technology and precision machining, the density and performance of the product are further improved, ensuring the stability of welding quality.
2. Beryllium copper (BeCu): the choice of high strength
Compared with chromium-zirconium-copper, beryllium copper electrode materials have higher hardness, strength and softening temperature, but relatively low conductivity.
Performance characteristics: Beryllium copper electrodes are suitable for welding sheet parts with high pressure and harder materials, such as rolling welding wheels for seam welding. At the same time, it has good elasticity and thermal conductivity, which is very suitable for manufacturing electrode accessories such as nut welding chucks.
Cost and application: Due to the high cost of beryllium copper electrodes, they are usually listed as special electrode materials. However, its excellent performance and wide application areas still make it occupy a place in the market.
3. Aluminum oxide copper (CuAl₂O₃): High temperature choice
Aluminum oxide copper is an excellent electrode material with excellent high-temperature mechanical properties, high strength and good conductivity.
Performance advantages: Aluminum oxide copper electrodes are particularly suitable for welding galvanized sheets, and will not produce the phenomenon of electrode and workpiece sticking, which effectively solves the problem of welding galvanized sheets. At the same time, it has strong wear resistance and long life, which further improves production efficiency and reduces production costs.
Market prospects: Although the cost of aluminum oxide copper electrodes is currently relatively expensive, given its excellent performance in galvanized sheet welding and the wide application of galvanized sheets, its market prospects are still very broad.
4. Tungsten (W) and molybdenum (Mo): the choice for special applications
Tungsten and molybdenum electrode materials have the characteristics of high hardness, high burning point and excellent high temperature working performance.
Performance characteristics: Tungsten electrode materials include pure tungsten, tungsten-based high-density alloys and tungsten-copper alloys; while molybdenum electrodes are suitable for welding non-ferrous metals such as copper, aluminum, and nickel due to their unique properties.
Application range: Tungsten and molybdenum electrodes play an important role in special application fields such as welding of copper braids and metal sheets of switches and silver spot brazing.
In summary, the selection of electrode materials and shapes of precision resistance spot welders has a vital impact on the quality, production cost and labor productivity of welded parts. In production practice, we should reasonably select electrode materials and shapes according to specific welding requirements and material characteristics to ensure the stability of welding quality and control of production costs.