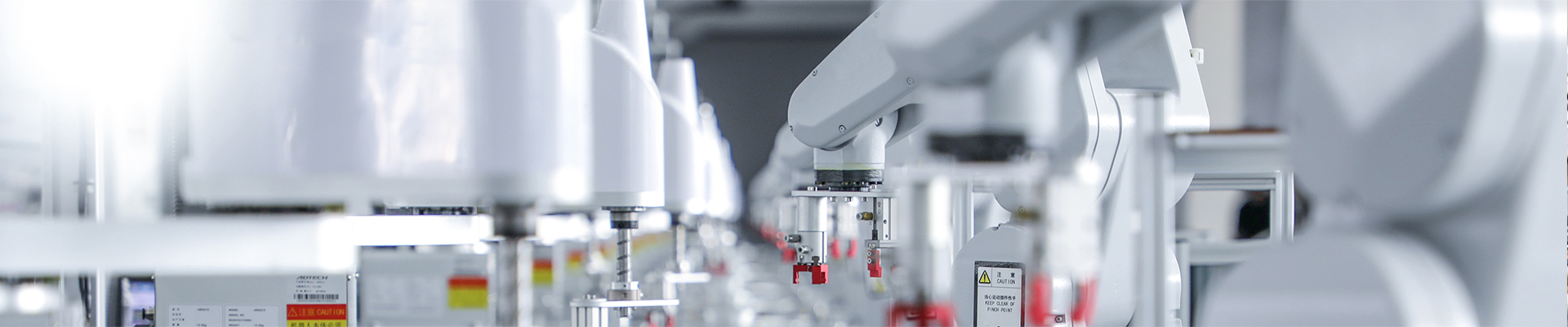
How to detect welding quality?
2024-11-23 15:02Welding is a process widely used in connecting various metal materials, and its quality directly affects the performance and service life of the product. Therefore, how to detect welding quality has become a very important issue. This article will introduce some commonly used welding quality detection methods.
1. Visual inspection
Visual inspection is the simplest and most intuitive welding quality detection method. By observing the color, shape, surface quality, etc. of the weld, the quality of the weld can be preliminarily judged. For example, the weld color should be uniform, the surface should be smooth and defect-free, and the weld width and height should meet the requirements.
2. Tensile test
Tensile test is an important method for detecting welding strength. Through tensile test, the tensile strength and elongation of the weld can be measured, and the strength and toughness of the weld can be evaluated. Qualified welds should have sufficient strength and elongation to withstand certain external forces.
3. Impact test
Impact test is an effective method to evaluate the impact resistance of welds. Through impact test, the impact absorption energy and impact toughness of the weld can be measured, and the toughness and impact resistance of the weld can be evaluated. Qualified welds should have sufficient toughness to withstand certain impact.
4. X-ray detection
X-ray detection is a non-destructive testing method that can penetrate metal materials through X-rays to observe the defects and structures inside the weld. X-ray detection can detect defects such as cracks, pores, inclusions, etc. inside the weld and evaluate the internal quality of the weld.
5. Ultrasonic testing
Ultrasonic testing is also a non-destructive testing method. Through the propagation and reflection of ultrasonic waves in metal materials, defects and structures inside the weld can be detected. Ultrasonic testing can detect defects such as cracks, pores, inclusions, etc. inside the weld and evaluate the internal quality of the weld.
6. Thermal shock test method (TPC)
Thermal shock test method is a method for evaluating the reliability of solder joints. Through short-term high-heat shock, the thermal shock effect that the solder joint may be subjected to in actual use can be simulated to evaluate the thermal shock resistance of the solder joint. Qualified solder joints should have sufficient thermal shock resistance and be able to withstand certain thermal shock effects.
7. Solder joint distortion detection
Solder joint distortion detection is a method for evaluating the quality of solder joints. By measuring the distortion of the solder joint, the deformation degree and stability of the solder joint can be determined. Qualified solder joints should have a small degree of distortion and be able to maintain a stable state.
8. Shear test
The shear test is a method of mechanically shearing the solder joint and evaluating the strength of the solder joint by testing the changes in force and displacement. The shear test can measure the shear strength and deformation of the solder joint and evaluate the bearing capacity and stability of the solder joint. Qualified solder joints should have sufficient shear strength and stability to withstand certain external forces.
The above methods can detect the welding quality of resistance welding, and the appropriate method can be selected for detection according to the actual situation. At the same time, it is also necessary to pay attention to the control of process parameters and operating specifications during the welding process to ensure the stability and reliability of welding quality.
In fact, the Huandian welding detector can be used to detect welding quality. Welding analyzer equipment has a self-developed 8-inch high-definition touch screen, which can display the real welding waveforms such as current, voltage, power, etc. of each welding in real time, as well as the corresponding welding data. Welding testing equipment can detect various types of resistance welding machines to help improve welding quality. Welding quality inspection device can monitor and determine key values such as welding current, voltage, power, welding time, pressure, displacement, etc., and save about 5 million key welding data to prevent welding instability and cause defective products to flow into the next process.