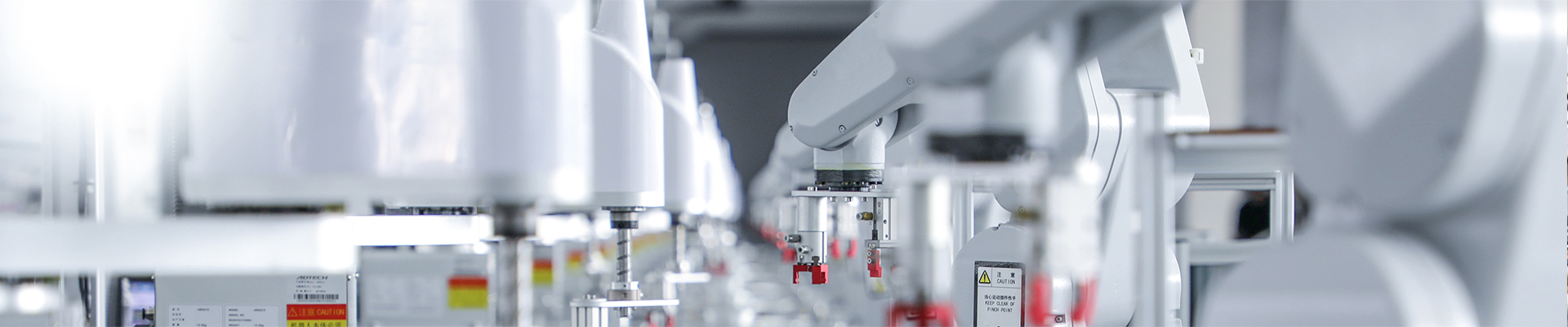
IDP 300 high precision resistance welding power supply an innovative benchmark for intelligent welding solutions
2025-02-20 18:46In the field of industrial manufacturing, welding accuracy and efficiency directly affect product quality and production costs. With its innovative technical architecture and intelligent control capabilities, Huandian IDP-300 high-precision resistance welding power supply is becoming the preferred equipment for industries such as automotive parts, electronic components, and new energy equipment, redefining the industry standard for precision welding.
1. Core technology breakthrough: precise and controllable digital core
Multi-mode intelligent control
Equipped with 6 control modes (constant current/constant voltage/constant power/constant peak current/constant pulse width/mixed control), resistance welding power supply can adapt to various process requirements such as spot welding, projection welding, and seam welding. Supports 1KHz-5KHz high-frequency pulse adjustment to meet the welding consistency requirements of complex working conditions such as copper and aluminum dissimilar metals and coating materials.
Servo pressure closed-loop system
The industry's first servo motor pressure control technology achieves 0.01N pressure accuracy and completely solves the impact force problem of cylinder welding. The displacement sensor monitors the penetration depth in real time, automatically interrupts abnormal welding processes, and improves the yield rate by more than 30%.
Visual data monitoring
The built-in 8-channel oscilloscope can simultaneously display waveform curves such as current, voltage, power, and resistance, and generate welding data reports. Supports SPC statistical analysis functions to provide quantitative basis for process optimization.
2. Scenario-based application value: driving industrial upgrading
New energy vehicle field
In the welding of power battery tabs, IDP-300 controls the heat input through multi-segment cycle pulse technology to avoid overburning of nickel sheets and significantly improve the safety performance of the battery cell. The measured data of a leading battery manufacturer shows that the welding spatter rate is reduced to less than 0.5%.
Precision electronic manufacturing
For the micro-welding needs of micro relays and sensor leads, the equipment supports 0.5ms time resolution and 5A micro-current control, achieving traceless connection of wires below φ0.1mm, meeting the cleanliness requirements of medical electronic devices.
Automated production line integration
Equipped with industrial bus interfaces such as EtherCAT and PROFINET, precision resistance welding power supplies can be seamlessly connected with robotic arms and PLC systems. The pressure-current-time collaborative control algorithm shortens the welding cycle to 0.3 seconds per point, helping to improve the efficiency of the automotive welding line by 18%.
3. Sustainability guarantee: long-term and stable value creation
The IGBT module and triple heat dissipation system design support 24-hour continuous operation; the overvoltage/overcurrent/short-circuit protection response time is less than 1μs, and the equipment MTBF (mean time between failures) exceeds 50,000 hours. The supporting cloud management system can also realize remote diagnosis and process parameter sharing, reducing operation and maintenance costs by 40%.
As an innovator in the field of high-precision welding, Huandian IDP-300 is reconstructing the production boundaries through digital and intelligent technologies. For detailed equipment parameters or industry solutions, please visit the official website to view the complete technical white paper.