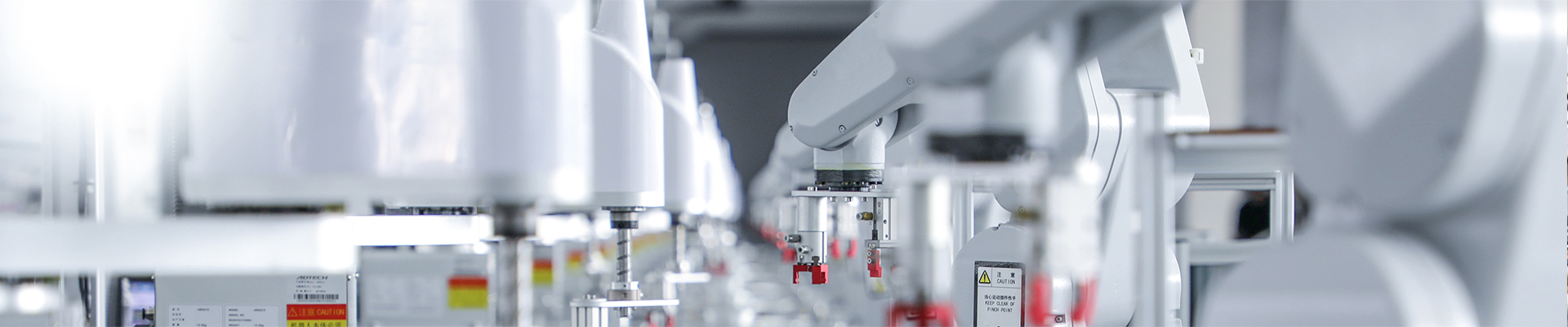
Introduction to the welding advantages of precision resistance welding
2024-09-29 15:18Precision resistance welding is a method of pressing the workpiece to be welded between two electrodes and passing an electric current through it, using the resistance heat generated by the current flowing through the contact surface of the workpiece and the adjacent area to heat it to a molten or plastic state to form a metal bond. In spot welding, the workpiece is only welded on a limited contact surface, the so-called "spot", and forms a flat spherical fusion. Spot welding can be divided into single spot welding and multi-spot welding. In multi-spot welding, more than two pairs of electrodes are used to form multiple nuggets in the same process.
Seam welding is similar to spot welding. In seam welding, the workpiece passes between two rotating disc electrodes (rollers) to form a continuous weld with the front and back overlaps of the strip welding points. Projection welding is a variation of spot welding. There is a prefabricated convex point on a workpiece. In projection welding, one or more nuggets can be formed at the joint at one time. In butt welding, the end faces of the two workpieces are in contact, and after resistance heating and pressurization, they are welded along the entire contact surface.
Precision resistance welding has the following advantages:
① When the nugget is formed, it is always surrounded by a plastic ring, the molten metal is isolated from the air, and the metallurgical process is simple.
② The heating time is short, the heat is concentrated, the heat affected zone is small, the deformation and stress are also small, and usually no correction and heat treatment procedures are required after welding.
③ No filler metals such as welding wire and welding rods, as well as welding materials such as oxygen, acetylene, and argon are required, and the welding cost is low.
④ Simple operation, easy to achieve mechanization and automation, and improved working conditions.
⑤ High productivity, no noise and harmful gases, in mass production, can be compiled into the assembly line together with other manufacturing processes. However, flash welding needs to be isolated because of spark splashing.
IDP series inverter DC welding power source, as a masterpiece independently developed by Huandian, integrates high-frequency inverter and advanced DSP control technology. The core components are selected from imported components to ensure the excellent performance and long-term durability of the product. Its high-precision control system (accuracy up to 0.2 ms), low-heat design, micro-damage treatment of workpieces, beautiful weld appearance, strong welding tension and high stability all demonstrate Huandian's ultimate pursuit of welding quality. At the same time, the power source also has comprehensive data monitoring and quality traceability functions, providing strong support for lean production in modern manufacturing.