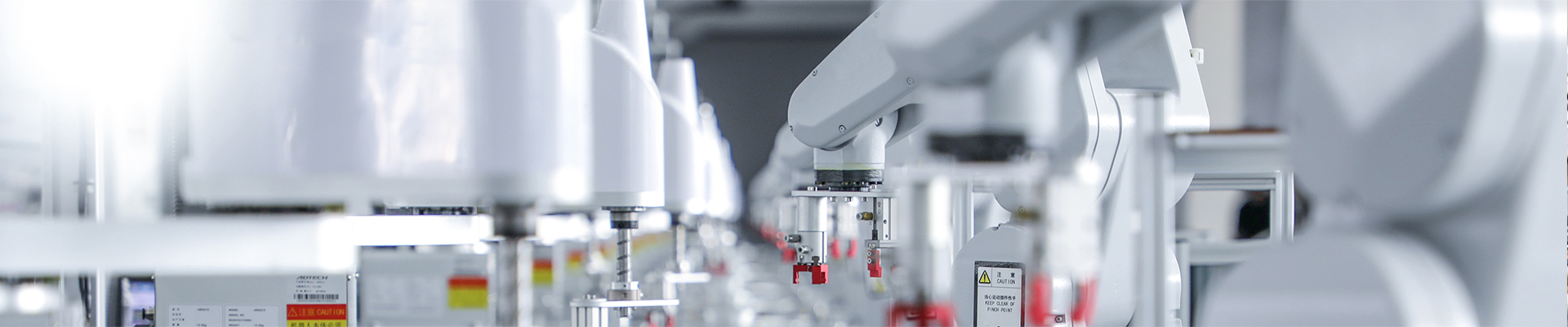
Resistance welding controller automatic welding solution application
2024-12-02 11:28The resistance welding process, with its unique current heating and fusing mechanism, has demonstrated extraordinary skills in the field of welding metal workpieces. The core of this process lies in the perfect integration of high-precision current control and welding functions, which has enabled many products' welding automation production lines to adopt resistance welding controllers to accurately complete welding tasks. Among the common metal elements, steel, iron, copper, aluminum, etc., can all achieve firm and beautiful welding through this technology.
The resistance welding controller is not only powerful, but also has the convenience of external interface communication, which has brought great convenience to the work of automation engineers. Engineers can easily debug and control these controllers, just need to design the matching structure and production line layout according to the characteristics of the welding product. The compact structure of the controller makes sup welding controller possible to flexibly arrange robot welding controller on the production line, whether control for resistance spot welding is placed at the bottom or on a simple bracket.
The advantages of the resistance welding process are also significant. Electric resistance welding is particularly suitable for welding precision metal parts, without the need for additional welding consumables, reducing production costs. At the same time, the adjustment of welding parameters is controllable and unrestricted, providing engineers with great freedom of operation.
However, any technology has its limitations. Resistance welding has certain limitations on welding thickness. For metal parts that are too thick or too thin, the welding effect may not be satisfactory. In addition, high efficiency inverter resistance welding machine is not suitable for welding highly conductive metal materials and operating in a small space.
However, despite this, the application prospects of resistance welding technology in automated welding production lines are still broad. In theory, as long as the thickness of the metal product is between 0.1mm and 9mm, engineers can design the corresponding automated welding production line according to customer needs. After the production line design is completed, the welding part only needs to reserve enough space and structure, and the welding controller can be debugged separately to ensure that the welding quality reaches the best state. Such a flexible and efficient welding process will undoubtedly bring a better future to the metal processing industry.