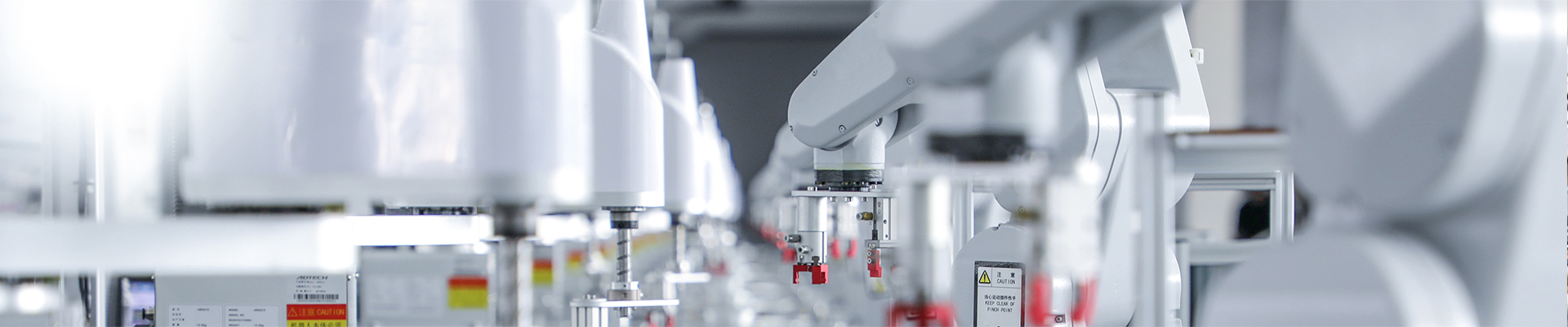
What are the reasons for instability during the welding process of precision spot welding machines?
2024-10-17 15:42Regarding the question of how to weld chip inductor hollow coils, enameled wires, and copper wires with precision spot welding machines, the editor has summarized some experiences for your reference.
Why does the enameled wire appear in the welding process always explode or have no molten core at all, or burn directly? The main reasons are as follows:
1. The current is too large and the time is too long, which will definitely cause explosion or spatter. The unstable factor of the power supply is almost zero, unless there is an alarm, which is another matter;
2. The pressure of the enameled wire is too small or unstable during welding, which is easy to splash or explode. This reason is easily overlooked by many manufacturers. The welding effect is not good, and the power supply is always blamed. In fact, at the moment of welding discharge, the pressure of the upper and lower electrodes is a very important factor. The so-called welding pressure does not refer to the maximum pressure that the cylinder can provide. Welding Presure refers to the pressure of the electrode at the moment of welding. This needs to be controlled accurately. The most ideal state is to use a pressure sensor device to discharge the power supply signal when the preset pressure is reached. Instead of notifying the power supply to discharge through a delay signal. Because of the delay control, the requirements for each machine adjustment master are different. If the springs on the mechanical structure are also different, welding pressure will be even more unstable. Some machines have cylinders that press down quickly, while others have cylinders that press down slowly. For cylinders that press down quickly, the spring compression is greater in the same amount of time, so the electrode pressure provided at the moment of welding is also greater. The smaller the contact resistance between the corresponding electrodes, the greater the current required to weld firmly, or even there is no way to weld firmly.
3. The precision spot welding machine does not peel the enameled wire cleanly, or in serious cases, you only peel one side. Recently, a customer used laser peeling, which means that the peeling is not clean, because a laser can only irradiate one side of the enameled wire. In this case, it is inevitable that you use the old power supply shown in the figure, because welding machine does not have a pre-welding inspection function. Our latest inverter welding power supply has a pre-welding function, that is, a pre-welding inspection function. Before each coil is officially discharged, I will weld enameled wire with a small current and measure its resistance. The peeling is definitely not within the range of good products. Next, the welding power supply of this product automatically alarms, and you can choose not to weld, which effectively avoids the possibility of welding explosion and electrode explosion, and you don’t have to grind the electrode so frequently.