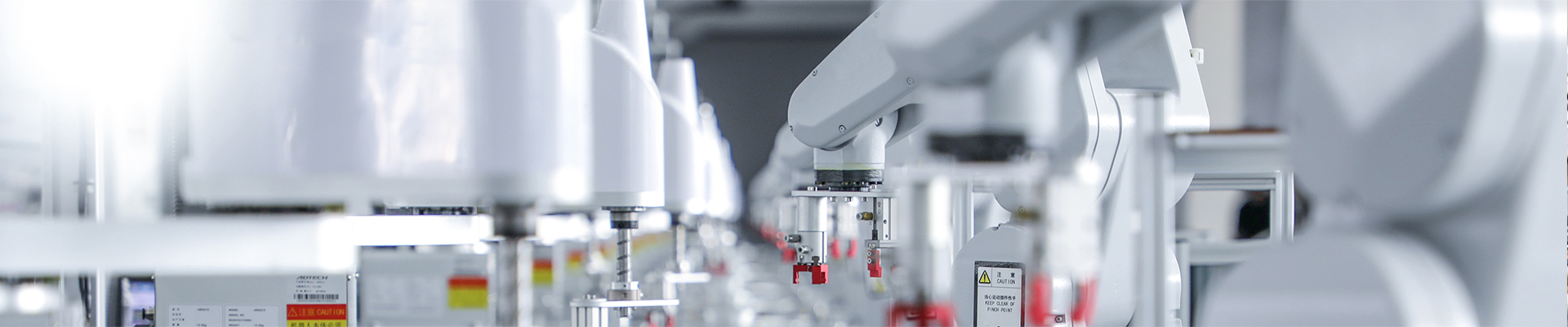
Why do we need to use precision spot welding machines to weld precision workpieces?
2024-12-24 11:16In the diverse world of industrial manufacturing, precision spot welding machines are undoubtedly a highly regarded "star craftsman". With its excellent performance, spot welder is widely active in many fields, especially in the welding of precision workpieces, showing irreplaceable value.
Precision spot welding machines belong to the category of spot welding machines and are customized for small and precise workpieces. Small precision workpieces are usually "small in size and thin in texture", which makes their requirements for resistance welding parameters almost harsh. As the elite force of resistance welding equipment, precision spot welding machines focus on the three elements of resistance welding - heating energy, heating speed, welding current (waveform), welding time and pressure, and implement fine control. Compared with ordinary spot welding machines, hanging spot welder is the ultimate in the precise grasp of parameters, just like a master of micro-carving carving a masterpiece, ensuring that every welding is perfect.
Precision workpieces are like fine puzzles in the microscopic world, and are often seen in cutting-edge industries such as electronic component manufacturing, electronic equipment, instrumentation, and medical equipment. These micro-workpieces are small in size, and foils and wires with a thickness or diameter of ≤0.1mm are often found at the joints. The spot welding position is narrow, and the materials are special and often covered with Au, Ag, Ni and other coatings. Kovar, molybdenum alloy, beryllium bronze, etc. are all "frequent visitors". Although they are small in size, they carry the key mission of the take-off of modern high-tech industries.
When micro resistance spot welding comes to welding micro-workpieces, there are many challenges, but there are also ways to deal with them.
On the one hand, micro-workpieces with small thermal inertia have scarce heat generation and rapid heat dissipation during welding. Unlike workpieces with large thermal inertia, their temperature fluctuates greatly with the instantaneous value of current. For this reason, welding requires a large current waveform pulse amplitude and a short power-on time. The medium-frequency inverter technology can accurately "adapt" and stabilize the current to ensure welding quality.
On the other hand, when micro-workpieces are heated, there is little heat generation and strong heat dissipation, resulting in a small temperature gradient in the welding area along the thickness direction, and the temperature of the bonding surface is similar to that of the outer surface, making it difficult to heat it in a concentrated manner, especially for metals with excellent thermal conductivity. When welding thin parts or metals with good thermal conductivity, the thermal inertia is smaller and the current waveform has a greater impact. Therefore, the precision spot welding machine needs to accurately control the current waveform, and at the same time, carefully control the electrode pressure, the surface state of the weldment, the electrode shape, etc. to ensure that the welding area forms an ideal temperature gradient.
Furthermore, in addition to the traditional melting connection, the micro-workpiece welding joint also allows solid-phase connection. The fitting surface does not melt, and it relies on full recrystallization and diffusion to "hold hands". Although the strength fluctuates, inverter resistance welding machine can meet the electrical and magnetic requirements of the micro-workpiece. Spot projection welding machine is suitable for spot welding of dissimilar metals, special metal welding, and traceless welding scenes with strict appearance requirements.
With its exquisite control of welding parameters, the precision spot welding machine has been galloping in the field of precision workpiece welding, adding a strong and colorful touch to the delicate chapter of modern manufacturing.