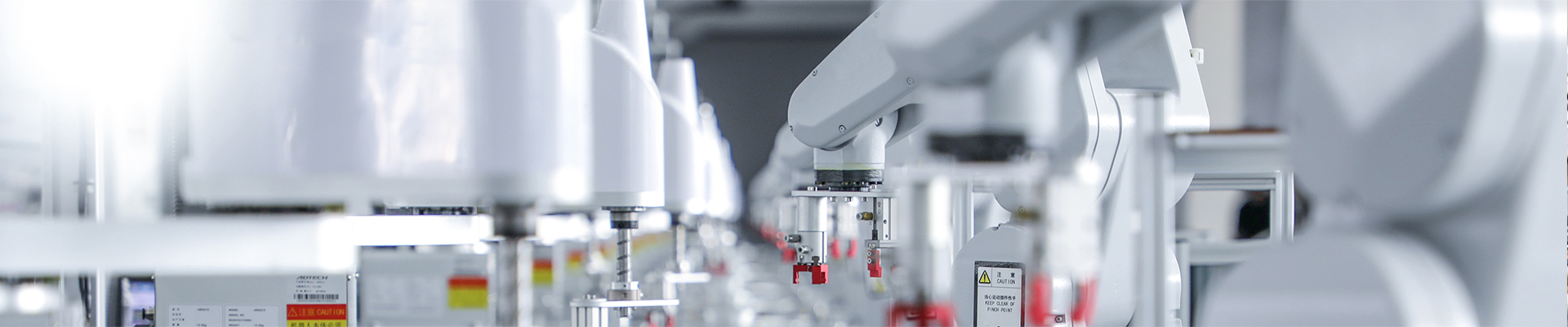
Comprehensive analysis of resistance welding transformer technical characteristics and performance
2025-03-22 14:52Resistance welding transformers have high welding efficiency, fast speed, strong weldment, reduce welding costs, and are suitable for welding a variety of materials. Resistance welding transformers are suitable for AC power with a rated frequency of 50-60 Hz and a voltage below 1000V. They are mainly used in spot welding machines, seam welding machines and butt welding machines.
I. Technical characteristics
(1) High current and low voltage process characteristics
Resistance welding uses resistance heat as the heat source. Welding machine transformer's core technical feature is the use of high current (2000-40000A) combined with low voltage welding. Since the workpiece resistance value is usually less than 100μΩ, sufficient heat must be generated by ultra-large current to achieve effective welding.
(2) High power control system
The supporting welding inverter transformer capacity is usually more than 50kVA, and a special winding design (single-turn or double-turn structure) is adopted to achieve power output control by adjusting the number of turns of the primary winding. Although this design simplifies the welding inverter transformer structure, welding inverter transformer also limits the flexibility of power regulation.
(3) Non-continuous load operation characteristics
The welding circuit adopts a unique pre-closure design: before the mfdc welding transformer is powered on, the workpiece clamping and circuit closure are pre-completed. This working mode eliminates no-load energy consumption (except for flash butt welding process), and the loading and unloading, positioning, pre-pressing and other processes in the welding cycle are all completed in the power-off state.
2. Technical advantages
(1) Metallurgical quality assurance
The nugget formation process is completely wrapped by the plastic metal ring, which realizes the physical isolation of the melting zone and the air, effectively simplifies the metallurgical reaction process, and ensures the stability of welding quality.
(2) Excellent heat-affected zone control
The concentrated heating characteristics (heating time ≤ 0.1 seconds) control the heat-affected zone range to 0.5-2mm, significantly reducing residual stress and welding deformation. Most workpieces do not need correction and heat treatment after welding.
(3) Outstanding economic efficiency
No welding material consumption (welding wire, welding rod, shielding gas, etc.) is required, and the welding cost is reduced by about 40% compared with the traditional process. The equipment has a high degree of automation, and the welding volume per shift can reach 800-1200 pieces.
(4) Environmental advantages
There is no open flame or smoke emission in the whole process, and the noise value is ≤ 65dB (A), which meets the industrial environmental protection standards. Welding machine transformer is particularly suitable for automated production line integration and can realize multi-process synchronous operation.
3. Technical limitations
(1) Quality inspection challenges
A mature non-destructive testing system has not yet been established. Currently, quality is mainly ensured by destructive testing and process monitoring, which increases the difficulty of process control.
(2) Joint performance constraints
Spot weld lap joints have inherent structural defects: the angle around the weld nugget causes stress concentration, which causes the tensile strength to decay by about 15-20%, and the fatigue life is only 60-70% of that of continuous welds.
(3) Equipment operation and maintenance costs
The initial investment of high-power equipment (typical configuration 400kVA) is high, and single-phase AC welding machines are prone to cause grid imbalance problems. The precision servo system increases the complexity of maintenance, and the replacement cost of key components (such as thyristor modules) exceeds 25% of the total equipment price.
4. Technology Evolution Direction
The new generation of resistance welding equipment is breaking through the existing limitations through the following technological innovations:
Development of real-time quality monitoring system based on infrared thermal imaging
Introduction of pulse current technology to optimize joint microstructure
Use of three-phase rectification technology to improve grid compatibility
Design of modular power units to reduce maintenance costs
These improvements have enabled resistance welding to show broader application prospects in emerging fields such as new energy vehicle battery packs and aerospace precision parts manufacturing.