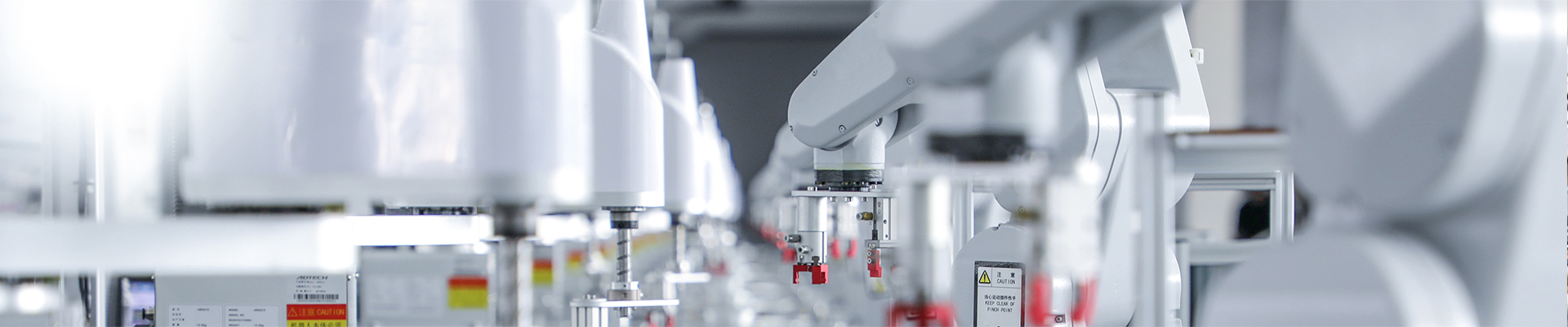
Functional features of inverter welding controller
2024-12-10 10:59In the brilliant world of resistance welding, Huandian inverter precision welding controller is like a dazzling technological star, shining with core light, leading the welding process to a new peak.
Spot welder controller presents six control modes ingeniously, just like having the unique skills of the six-pulse magic sword. Whether scr welding controller is the precise control of current in constant current mode, the stable control of voltage in constant voltage mode, or other complex welding demands, wtc weld controller can handle them with ease, and guarantee the stability and excellent quality of each welding with meticulous precision, just like putting an indestructible quality armor on the welding work.
Welding roller control five working frequencies, 1KHz, 2KHz, 3KHz, 4KHz, 5KHz, are like a smart scale, which can be selected and switched freely according to the diverse characteristics of welding materials, subtle differences in thickness, and unique standards of process requirements. Just like a music master, according to different rhythms of the movement, nadex welding controller accurately adjusts the most harmonious welding frequency melody, carves out the impeccable best welding results, and makes each welding point a vivid interpretation of the aesthetics of craftsmanship.
The servo motor control function is launched, like a precise master of mechanics, to achieve precise control of multi-stage welding pressure, cleverly resolve the troubles caused by the instantaneous impact of the traditional cylinder welding head, and inject a soft and stable force into the welding process. In addition, the welding head reset distance can also be set flexibly. Between the extension and contraction, the stability and quality of welding have been greatly improved unprecedentedly, making the welding process as smooth and natural as flowing water.
The gorgeous appearance of multi-stage welding combined cycle pulse discharge technology solves complex welding needs. Welding machine controller is like a wise welding magician, cleverly changing the combination and cycle of multiple welding parameters during the welding process, creating unlimited possible welding effects, and meeting the most stringent welding process challenges.
The stunning appearance of the exquisite human-machine touch interface brings a double feast of vision and touch to the operator. Resistance spot welding controller built-in oscilloscope and monitor functions seem to open a window for the welding process to see the microscopic world. Eight real waveforms and welding data such as current, voltage, power, and resistance are clearly presented and clear at a glance. The operator is like having a pair of wise eyes that can see through the fog of data, real-time monitoring, and precise control of every subtle change in welding quality, so that welding defects cannot hide.
The pressure displacement monitoring system is complete, and the pressure monitoring and triggering functions are like sensitive tactile nerves, which can always sense the subtle changes in pressure; the displacement monitoring and penetration interruption functions are like precise navigators, ensuring that the pressure and displacement are always on the accurate track during the welding process, and protecting the stability of welding.
What is more worth mentioning is that spot welding machine controller built-in database function is like a vast data treasure house, which can easily store about 5 million welding point data and support convenient export of USB flash drives. At the same time, the real-time monitoring of the average effective value and instantaneous value of current, voltage, and power is like installing an intelligent monitor for the welding process, which protects the stability and efficiency of the welding process from all directions and angles, comprehensively improves the welding quality and production efficiency, makes spot welding power controller shine in the field of resistance welding, and becomes a powerful engine to promote the continuous innovation and development of welding technology.