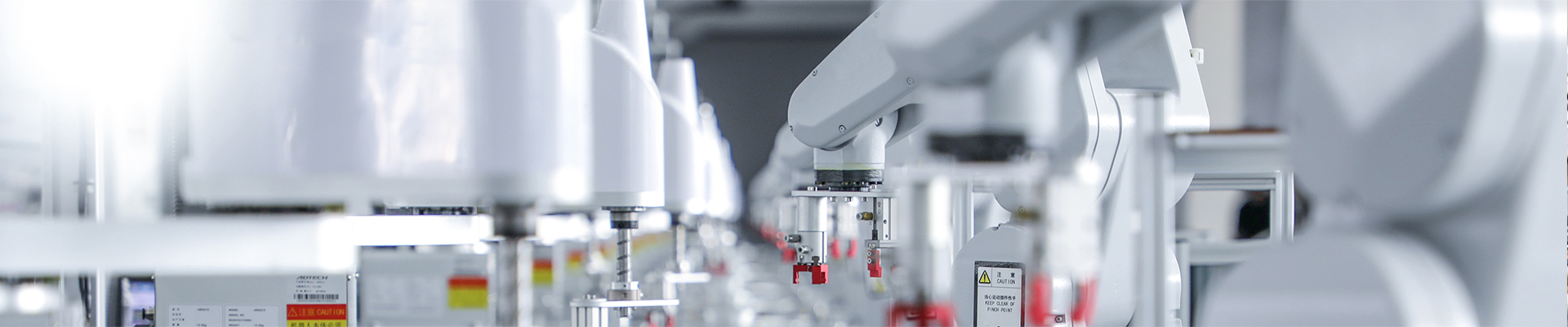
Importance of weld penetration detection
2024-12-07 15:40In the resistance welding process, the weld penetration refers to the depth of melting of the metal material in the welding area. This key parameter is closely related to welding current, welding time, electrode pressure and other factors, among which welding current is the most important factor affecting penetration depth. Normally, the larger the welding current, the deeper the penetration; the smaller the current, the shallower the penetration. In addition, electrode pressure also has a significant impact on penetration depth. Appropriate electrode pressure helps the metal to fully melt, thereby increasing the penetration depth, but excessive pressure may cause metal deformation in the welding area, which in turn reduces the penetration depth.
As an important welding process in the manufacturing industry, resistance welding is widely used in automobiles, aerospace, electronics and other industries because of its high efficiency, energy saving and environmental protection. As a core indicator of welding quality, weld penetration directly affects the strength, sealing and service life of welded joints. Therefore, accurate and rapid detection of weld penetration is crucial to ensure welding quality.
Nowadays, new spot weld testing equipment for weld penetration is constantly being introduced. For example, high-performance equipment such as Huandian welding quality inspection device can not only monitor key parameters in the welding process (such as welding current, pressure, voltage, welding time, etc.) in real time, but also have a variety of practical functions. The device can display and record welding information in real time and export data via USB to facilitate subsequent analysis and problem tracing. In addition, welding analyzer equipment is equipped with a welding quality judgment function that can set upper and lower limits for key parameters such as current, voltage, power, pressure and displacement for monitoring. Once a welding abnormality is detected, the equipment will immediately issue an alarm and automatically identify unqualified products to ensure the efficiency and reliability of the production process.
At the same time, the equipment supports large-capacity database storage, can record millions of welding data and historical alarm information, and supports exporting and generating tables through USB flash drives to facilitate welding quality control monitoring and traceability.
All in all, the detection of weld penetration is of great significance in the resistance welding process. Choosing appropriate welding monitor and methods can effectively evaluate welding quality and ensure high strength, good sealing and long service life of welded joints. With the continuous advancement of science and technology, more innovative detection technologies will continue to emerge to provide more reliable support for resistance welding quality control.