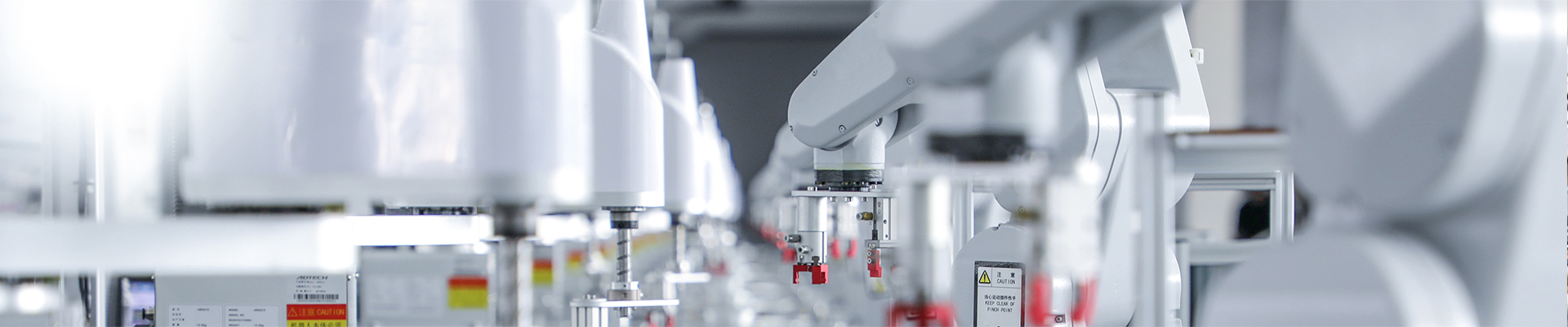
How to detect welding penetration?
2024-12-05 10:55The detection methods of welding penetration mainly include the following:
1. Metallographic microscope observation: After cutting or grinding the weld joint, use a metallographic microscope to observe the cross section of the weld. By checking the length and shape of the penetration line, the penetration can be preliminarily evaluated.
2. Compression test: Perform a compression test on the weld joint, observe the shape and position of the fracture surface of the specimen, and infer the degree of penetration. Usually, a deeper penetration will cause the weld stretching area to be located inside the base material.
3. Weld penetration microscope observation: Use a weld penetration microscope to observe the weld at high magnification to detect the size of the penetration, the structure of the fusion area and the grain structure. By analyzing the results of the microscope observation, it is evaluated whether the welding quality meets the requirements.
The working principle of the welding penetration detector is usually based on thermocouple technology. Taking the Huandian welding penetration detector as an example, it uses thermocouples to measure the temperature changes of the base material and the welding point during welding, as well as the current fluctuations. Thermocouples convert temperature changes into electrical signals and reflect temperature changes by measuring the voltage difference between the two ends. The computer system processes and analyzes this data and ultimately calculates the penetration of the weld.
The importance of the welding quality inspection device in resistance welding quality control is self-evident. First, resistance weld monitoring helps manufacturers determine the best welding parameters, such as current and time, to ensure the best penetration and welding effect. Second, by real-time monitoring of the welding process, potential quality problems, such as insufficient or excessive penetration, can be discovered in time to avoid production waste and product quality degradation. In addition, the tester can also provide important data on electrode pressure, material thickness, and thermal conductivity, helping to optimize the production process and improve efficiency and product quality.
HD-400B all-purpose welding detector is a resistance welding detector independently developed by Huandian. The main components are imported products to ensure the reliability and stability of the product. Through the digital collection and monitoring of key values in the welding process, it realizes the real-time collection, display, over-limit alarm and network communication of key values such as welding current and voltage of a single resistance welding device or multiple resistance welding devices during the welding process, and records and analyzes the data and traces the history. Achieve the purpose of standardizing welding operations and improving welding quality
Overall, the resistance welding penetration tester is a key tool to ensure welding quality, and can provide manufacturers with an effective means of real-time monitoring, production parameter optimization, and quality assurance.