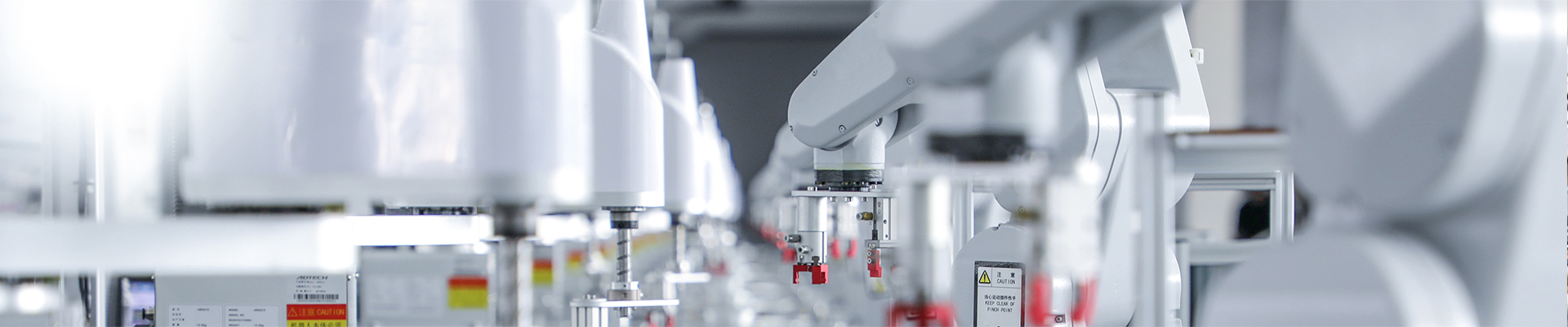
Inverter welding power supply for resistance welding
2024-08-28 15:59As an important achievement of modern welding technology, the inverter welding power supply for resistance welding not only provides stable and efficient welding current, but also incorporates many advanced intelligent functions, making the welding process more accurate and controllable. Among them, the exquisite human-machine touch interface, built-in oscilloscope and monitor function, pressure displacement monitoring and built-in database and other features have greatly improved the practicality and convenience of the inverter welding power supply for resistance welding.
First of all, the design of the human-machine touch interface of Huandian's inverter welding power supply makes the operation of the power supply more intuitive and simple. Users can easily adjust the welding parameters through the touch screen and monitor various data in the welding process in real time. This interface design not only improves work efficiency, but also reduces the difficulty of operation, making it easy for even non-professionals to get started. Secondly, the inverter welding power supply comes with an oscilloscope and monitor function, which can display 8 real waveforms and corresponding welding data such as current, voltage, power, and resistance in real time.
This function enables users to intuitively understand the changes in various parameters during the welding process, so as to better control the welding quality. By monitoring these data, users can promptly discover problems in the welding process and take corresponding measures to adjust them to ensure welding quality. In addition, the inverter welding power supply also supports pressure displacement monitoring, built-in pressure monitoring, pressure triggering, displacement monitoring, and displacement penetration interruption functions.
These functions enable the power supply to monitor the pressure and displacement changes during the welding process in real time, thereby ensuring the stability and consistency of the welded joint. When an abnormal situation occurs during the welding process, the power supply can automatically interrupt the welding process to avoid the production of defective products.
The built-in database function of the inverter welding power supply is also a highlight. The power supply can store the current, voltage, power, resistance, pressure, displacement and other values of about 5 million welding points, and supports USB flash drive export. This function enables users to easily record and analyze welding data, providing strong support for subsequent process improvement and quality control.
Finally, the inverter welding power supply can also monitor the average effective value and instantaneous value of current, voltage, and power to further control the welding quality. By monitoring and analyzing these data, users can more accurately grasp the dynamic changes of the welding process, thereby optimizing welding parameters and improving welding quality and efficiency. In short, the inverter welding power supply for resistance welding plays an increasingly important role in the field of modern welding with its high efficiency, stability, and intelligence. It not only improves welding quality and efficiency, but also reduces operating difficulty and cost, injecting new vitality into the production and development of the enterprise.