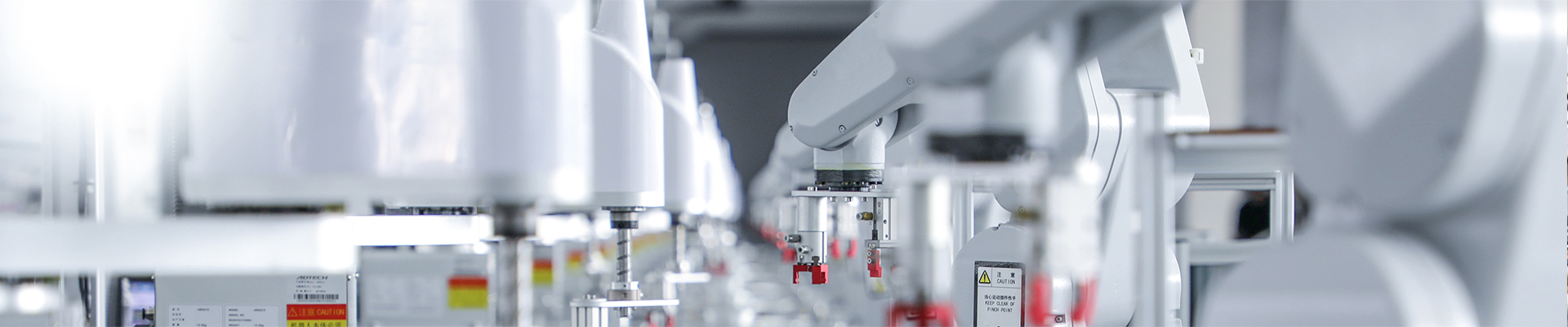
What is the difference between a precision spot welder and a seam welder?
2024-10-14 15:34Precision spot welder and seam welder: similarities and differences between the two
Precision spot welder, a device designed for high-precision welding needs, is widely used in the butt welding of fine parts such as sensors, LEDs and their leads, copper foil, enameled wire, relays, electronic sockets, and tungsten-molybdenum materials for electro-optical use. As an advanced form of resistance welding, the seam welder can easily achieve the overlap or butt joint of welded parts through its unique roller electrode design, and form a perfect continuous weld under continuous or intermittent pulse power supply.
So, what is the difference between these two devices?
First of all, from the electrode shape, we can see it at a glance. The electrode of the precision spot welder adopts a double-column design, which is very suitable for precise welding of overlapping plates. The seam welder, with its unique double roller electrode, stands out and becomes an ideal choice for manufacturing sealing box.
Secondly, in terms of welding methods, both have their own advantages. The precision spot welder uses the principle of double-sided double-point overcurrent welding to apply pressure to the workpiece through the electrode, so that the two layers of metal are instantly hot-melted under the action of contact resistance, and the welding current will not cause any damage to the internal structure of the welded workpiece during the process of forming a loop. The seam welder, on the other hand, pressurizes and rotates the weldment through the roller electrode, continuously or intermittently supplies power, thereby forming a continuous weld on the weldment.
In addition, the seam welder also shows its unique advantages in the application field. It is widely used in the manufacture of joints that require sealing, such as the welding of automobile fuel tanks, water tanks and other parts. At the same time, it can also be used to weld ordinary non-sealed sheet metal parts, and the thickness of the welded metal materials ranges widely, usually between 0.1 and 2.5 mm.
In summary, although both precision spot welders and seam welders are important equipment for resistance welding, there are obvious differences in electrode morphology, welding methods and application fields. Which equipment to choose depends on the specific welding needs and workpiece characteristics.
If you are eager to explore more knowledge or have a strong interest in our products, please contact us via WhatsApp or WeChat. We warmly welcome your consultation and look forward to providing you with detailed answers.