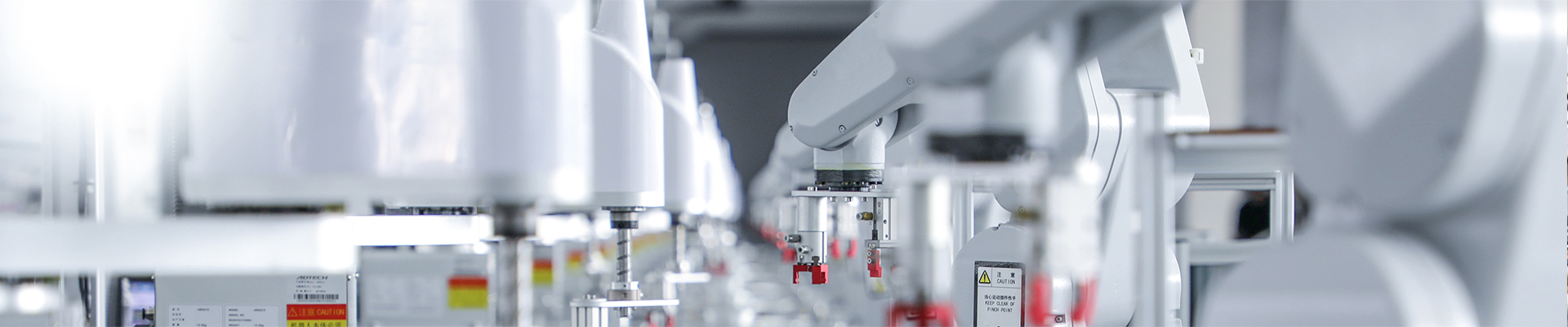
- Home
- >
- News
- >
- Industry news
- >
News
Resistance welding transformers have high welding efficiency, fast speed, strong weldment, and reduce welding costs. They are suitable for welding a variety of materials, such as aluminum alloys and aluminum and other materials with fast thermal conductivity and poor weldability. In addition, for the welding of galvanized sheets and ordinary multi-layer sheets, welding transformer's welding quality is also much higher than that of power frequency welding machines.
Automatic feeding nut spot welding machine, with high efficiency and precision welding, environmental protection and energy saving, is widely used in the fields of automobile, aerospace, electronics and rail transportation, helping to upgrade industrial manufacturing.
The precision spot welding machine adopts 0.2 ms high-precision control 6 and servo pressure system, combined with mechanical positioning and electrical signal detection dual anti-reverse technology, to achieve low thermal damage and high stability in nut welding. The strength of the weld point reaches more than 90% of the parent material, and the defective rate is less than 0.5%. It is widely used in high-precision manufacturing fields such as automobiles and electronics.
The projection welding nut error-proofing detector improves welding quality and efficiency, prevents errors, and helps efficient production. Projection welding nut error-proofing detector is a powerful assistant and high-quality equipment in industrial production.
Lithium battery spot welding equipment has gone through many generations of development, each with its own characteristics. Huandian DC inverter precision power supply, with its excellent performance and stability, optimizes output, improves stability and efficiency, and meets various welding needs. Despite technological advances, different spot welding machines still have their own capabilities.
When choosing a lithium battery spot welding machine welding power supply, you need to consider the welding effect, scope of application and cost. Capacitor energy storage, inverter and AC welding power supplies each have their own advantages, suitable for different scenarios and meet diverse needs.
Inverter spot welding power supply has high-quality service and full life cycle guarantee. Features in the new energy field: medium frequency inverter is energy-saving and efficient, suitable for high-precision welding; supports lightweight materials and prevents thermal changes; integrated monitoring, high safety standards; small size, improved automation.
Leading resistance welder manufacturers are showcasing innovations, including high-efficiency inverter welding machines, advanced welding power supplies, analyzers, and thermocouple spot welding equipment, revolutionizing industrial welding.
Huandian IDP-300 is a high-precision welding power source with 6 control modes and 5 operating frequencies. Resistance welding power supports multi-stage adjustable welding pressure and has a built-in database function, making it suitable for complex welding conditions.
Ur welder provide high power high frequency DC welding power supplies, resistance spot welders, resistance weld monitorings, and professional customized automotive suspension spot welding solutions to ensure efficient and stable welding.
In 2025, the welding equipment industry is moving towards a new stage of precision, efficiency, intelligence and greening. Technological innovation leads the industry upgrade, and the market demand is strong, which promotes the high-quality development of the industry.
Precision spot welding machines are divided into resistive, capacitive energy storage and laser spot welding systems, suitable for different industrial scenarios. Huandian Intelligence provides energy-efficient and intelligently controlled spot welding solutions to meet the needs of new energy, 3C electronics and other industries.