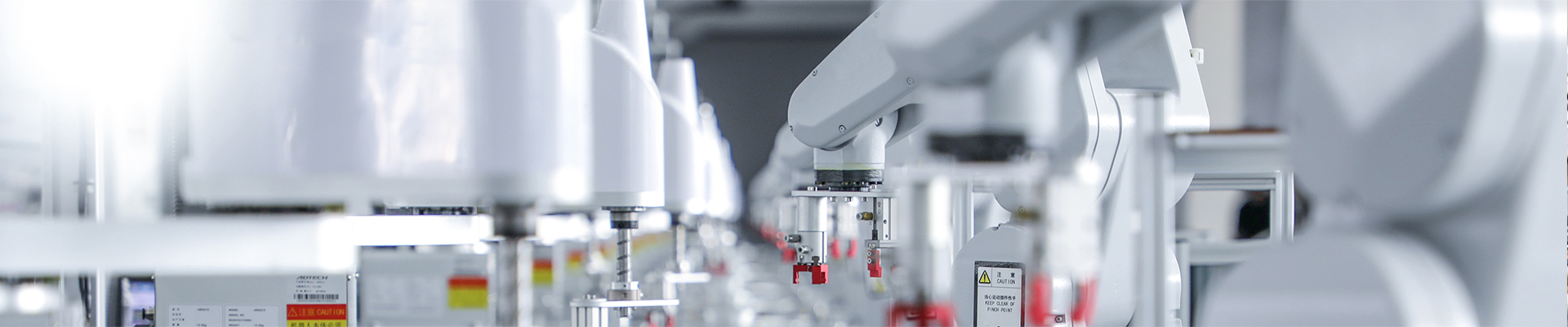
- Home
- >
News
The advantages of spot welding include high efficiency, high welding strength, and easy operation; the disadvantages are that the welding thickness is limited, the electrode is easily worn, it may cause deformation of the workpiece, and there are certain requirements for the shape and size of the workpiece.
Pedal operated spot welding machines are key equipment for precision welding in industry. They consist of a machine head, power supply and transformer. They are designed to be flexible and precisely controlled to ensure stable and efficient welding. The electrodes carry high current, maintain alignment and eliminate excess heat to ensure welding quality, making them an indispensable welding tool.
Spot welding, also known as resistance spot welding technology, uses the heat generated by current, resistance and power-on time to seamlessly fuse metal plates. Spot welding machine for sheet metal is widely used in various industries, especially in automated production lines and automobile manufacturing, demonstrating efficient and reliable welding quality.
When using the copper wire spot welding machine, you need to pay attention to equipment inspection, copper wire selection, safe operation and maintenance to ensure welding quality, operational safety and stable operation of the equipment.
When precision spot welding machines are welding materials such as enameled wires, it is necessary to pay attention to the precise control of current and time, the importance of welding pressure, and the quality of enameled wire stripping. Our latest inverter welding power supply has a pre-welding function, which can provide reminders before welding and improve welding stability.
The precision spot welding machine has good welding effect. When installing and using it, you need to pay attention to lead selection, safety protection, component tightening and oxide cleaning, ensure the normal voltage of the power grid, and pay attention to the maintenance of wearing parts.
Current detection of precision spot welding machines is the key to ensuring welding quality. Oscilloscope testing may not be accurate, so it is recommended to use a dedicated current tester for monitoring. When purchasing, companies should choose equipment equipped with a current tester and conduct regular testing and calibration to ensure the stability and reliability of welding quality.
Precision spot welders excel at welding fine components, while seam welders excel at producing continuous welds. The two have different electrode shapes, welding methods, and application areas.
The selection of electrode material and shape for precision spot welding machines is crucial, affecting welding quality, cost and efficiency. Materials such as chromium zirconium copper, beryllium copper, aluminum oxide copper, tungsten and molybdenum each have their own advantages and need to be selected as needed.
Copper wire terminal welding relies on a high-efficiency spot welding machine with a built-in special resistance welding transformer. Resistance spot welder uses the principle of resistance welding to achieve precise welding and ensure a firm connection.
IDP series inverter DC welding power source, as a masterpiece independently developed by Huandian, integrates high-frequency inverter and advanced DSP control technology. The core components are selected from imported components to ensure the excellent performance and long-term durability of the product. Its high-precision control system (accuracy up to 0.2 ms), low-heat design, micro-damage treatment of workpieces, beautiful weld appearance, strong welding tension